本文对混凝土泵送性能指标与检测方法进行了简单介绍,结合施工现场对混凝土可泵性进行简易评价的要求,提出了用坍落度筒检测数据评价混凝土可泵性的参考指标;并对影响混凝土可泵性的主要因素和改善措施进行了阐述。
泵送混凝土是商品混凝土企业的主要产品,泵送混凝土是可通过泵压作用沿输送管道强制流动到目的地并进行浇筑的混凝土[1]。商品混凝土企业大部分建在城区以外,新拌混凝土经搅拌、运输和一定的时间间隔,才能到达工地。运抵现场的混凝土拌合物与出机时相比,和易性发生了不同程度的变化。为了避免泵送失败,现场评价混凝土的可泵性,分析影响可泵性的因素,并提出改善措施,显得十分重要。为此,笔者将自己的学习体会和实践经验归纳如下,仅供同行参考。
1、混凝土泵送性能指标及评价方法
混凝土可泵性是表示混凝土在泵压下沿输送管道流动的难易程度以及稳定程度的特性[1]。可泵性要求:混凝土拌合物在泵腔内易于流动,以充满所有空间;有良好的粘聚性、保水性,在泵送过程中不分层、不离析、不泌水;混凝土拌合物与管壁之间以及混凝土内摩擦阻力较小[5]。泵送性能指标包括:坍落度、扩展度和摩擦阻力(表征流动的难易程度),压力泌水值(表征流动的稳定程度)。混凝土可泵性与混凝土拌合物的和易性相对应。
1.1混凝土可泵性的试验室评价方法
评价可泵性,目前国际上尚无统一的方法,我国《普通混凝土拌合物性能试验方法标准》(GB/T50080—2002)[2]中规定,用压力泌水试验的方法进行检测。混凝土企业试验室普遍用坍落度、扩展度和压力泌水率来评价混凝土的可泵性。我国专家学者在这方面也进行了不少的研究[4-5],并积累了一定经验和数据。
1.2混凝土可泵性的现场评价方法
用坍落度筒和秒表可以在混凝土入泵前进行现场测试:用坍落度、扩展度评价流动性;用1250px 扩展时间、坍落度与扩展度比值评估摩擦阻力;用静置 30s 泌浆宽度(mm)评估稳定性[6]。在工程实践中,不同强度等级的混凝土可泵性差异很大:低强度等级不粘,稳定性差;中等强度等级对环境比较敏感;高强度等级太粘,摩擦阻力大。表1 为评价入泵混凝土可泵性的参考指标,对不同的泵送高度、不同的泵送方向,可泵性参考指标应是不同的。由于地区材料的差异性很大,此表仅供同行在工程实践中参考。
表1 入泵混凝土可泵性参考指标
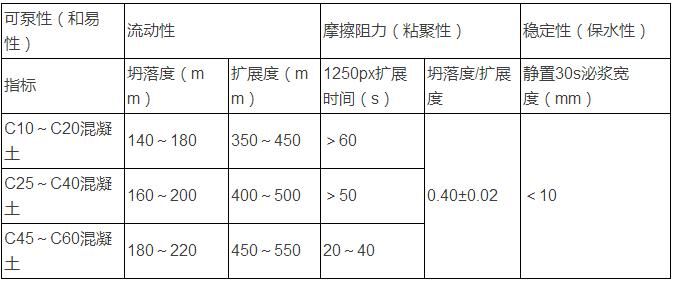
2、影响混凝土可泵性的主要因素
修订后的《混凝土泵送施工技术规程》(JGJ/T10—2011)[1],为了与现行有关标准协调,取消了“泵送混凝土原材料和配合比”的有关条文,但泵送混凝土的可泵性与混凝土原材料和配合比密切相关。
2.1配合比参数对可泵性的影响
2.1.1粉体体积的影响
粉体体积的大小影响混凝土的粘聚性。特别是低强度等级混凝土,由于水胶比较大,常因粉体体积不足,使得坍落度难以控制,造成混凝土离析而失去可泵性。
2.1.2水胶比的影响
水胶比表征浆体的稠度,水胶比降低时,浆体稠度增加,一般均引起浆体粘着系数增大,摩擦阻力随之增大;但水胶比变大时,浆体稠度减小,容易发生离析、泌水,造成拌合物不均匀而引起堵管。
2.1.3浆骨比的影响
浆骨比适当时,浆体填充骨料颗粒间的空隙并包裹着骨料,在骨料表面形成浆体层,在泵送管道内壁形成的薄浆层可起到润滑层的作用,使泵送阻力降低,便于泵送。浆体量大时,浆体层的厚度增大,骨料移动的阻力就会减小,混凝土流动性增大;浆体量太少时,浆体层的厚度减小,摩擦阻力增大,泵送困难。
2.1.4砂率的影响
合理的砂率可以使相同浆体量达到最大的流动性,或达到相同流动性时胶凝材料用量最少。砂率过大,骨料的总表面积和空隙率均增大,骨料间的浆体层减薄,流动性差,拌合物干稠,摩擦阻力增大,泵送困难;砂率过小,砂子不足以填充粗骨料间的空隙而需额外的浆体补充,骨料表面的裹浆层变薄,石子间内摩擦阻力增大,拌合物的流动性降低,稳定性变差,使粗骨料离析、浆体流失,会造成堵泵、堵管。
2.2原材料对可泵性的影响
2.2.1胶凝材料的影响
胶凝材料的品种、细度、矿物组成等,对达到同样流动性的混凝土需水性、保持流动性的能力、泌水特性、稠度影响差异较大,是影响可泵性的重要因素。特别是铝酸三钙、铁铝酸四钙含量和硫酸根离子含量,影响与泵送剂的相容性,影响新拌混凝土保持流动性的能力。
2.2.2粗细骨料的影响
粗骨料粒径大小、颗粒形状、级配组成、空隙率、吸水性能影响混凝土的可泵性,颗粒圆润、表面光滑的石子,空隙率小、表面积小,填充空隙和包裹颗粒所需的浆体较少,相同浆体量时,裹浆层和管道润滑层厚,流动性大、摩擦阻力小,对可泵性有利。
细骨料比粗骨料对可泵性的影响作用大。细骨料宜采用中砂,其通过公称直径315μm 筛孔的颗粒含量不宜少于15%,这部分砂对浆体的流动性、粘聚性、保水性、含气量等影响作用极大,极易影响混凝土的可泵性。
2.2.3泵送剂的影响
泵送剂是一种综合性的外加剂,是泵送混凝土不可缺少的重要组分,它在解决混凝土流动性和稳定性这一矛盾的两个方面扮演着重要角色。减水组分,起扩散润滑作用,能提高混凝土的流动性;缓凝组分,减缓水化反应进程,能抑制坍落度经时损失;增稠保水组分,增加浆体稠度,能提高混凝土的稳定性;引气组分,减小摩擦阻力,能提高混凝土的流动性。泵送剂内各组分的匹配是否合理,泵送剂的使用是否适当,都会影响混凝土的可泵性。
2.3和易性劣化对可泵性的影响
2.3.1坍落度损失对可泵性的影响
新拌混凝土的坍落度直接表征了混凝土的流动性,较大的坍落度损失,会降低混凝土的流动性,增加摩擦阻力,直接影响混凝土的可泵性。
2.3.2离析与泌水对可泵性的影响
新拌混凝土体系是由不同大小、不同密度的颗粒和水均匀拌成的混合物。离析与泌水破坏了混凝土体系中各组分的均匀分布,使混凝土组分丧失了连续性和稳定性,直接影响着混凝土的可泵性。
2.3.3时间及环境对可泵性的影响
新拌混凝土经搅拌、运输和一定的时间间隔,才能到达工地,这时混凝土的流动性和稳定性,都会在环境温度和湿度、运输时间的作用下发生不同程度的劣化,这直接影响着混凝土的可泵性。
3、改善混凝土可泵性的具体措施
混凝土流动性的增加往往造成稳定性的下降,同样,为增加混凝土的稳定性,减少离析、泌水程度,必须以降低流动性来实现。因此,改善混凝土可泵性的具体措施,应从解决好这一矛盾的两个方面着手。
3.1调整配合比,提高入泵混凝土的流动性和稳定性
及时掌握入泵混凝土的可泵性,根据有关技术条件调整配合比,使拌合物和易性得到及时、针对性的改善,即防止离析、减少泌水、抑制流动度损失。配合比的调整,要基于入泵混凝土的可泵性,并与拌合物的出机和易性、入模浇注的工作性联系起来进行分析,要使和易性、可泵性、工作性相辅相成。调整后的混凝土拌合物不仅要满足强度和耐久性的要求,还要注意与经济性的协调[3]。
对低强度等级的泵送混凝土,宜提高砂率,增加粉体体积,提高拌合物的粘聚性;增加泵送剂中增稠、保水、引气组分,提高拌合物的稳定性。对中强度等级的泵送混凝土,宜通过调整泵送剂中的缓凝组分,来抑制混凝土坍落度损失,保持混凝土的流动性。对高强度等级的泵送混凝土,宜降低砂率,增加泵送剂中高效减水组分的含量,或适当调整用水量,提高混凝土的坍落度和流动性,减小泵送阻力。
3.2优选原材料,提高混凝土的和易性和保坍性
注意选用需水量小的原材料,特别关注水泥的标准稠度用水量,粉煤灰、矿粉的需水量比,砂石的含泥量和吸水率。注意选用颗粒形状、级配组成优良且空隙率小、表面积小的骨料,特别关注粗骨料的粒形和空隙率,最大粒径要适应相关技术条件;特别关注砂的细度模数和空隙率,低强度等级选用细砂,高强度等级选用粗砂。注意泵送剂与混凝土流动性和稳定性的协调,特别关注泵送剂与混凝土其他组分的相容性,及泵送剂内各组分含量随季节的变化性。
3.3加强现场管理,保障泵送作业的连续性
泵送混凝土的生产、运输、泵送各环节都要认真执行《混凝土泵送施工技术规程》(JGJ/T10—2011)[1]。一定要加强泵送作业现场与搅拌站、运输车的协调和联络,要压缩来料待卸时间,更要减少泵送待料时间。夏季注意对泵管的冷却润滑,冬季注意对泵管的预热润滑。
搅拌作业必须保证混凝土生产的即时性和连续性。在夏季高温干燥时,为控制出机混凝土的温度、减小混凝土坍落度的经时损失值,要增加粗骨料洒水降温次数,保持粗骨料的饱和面干状态;要控制水泥温度,避免即进即用,因为粉体在储罐内是后进先出。
运输作业要听从现场调度的指挥,加强与现场、搅拌楼的协调联络,及时通报运输路线的通行状况,保证混凝土运送的及时性和准确性。
4、结语
影响混凝土可泵性的因素和机理是多变的,混凝土可泵性评价是一个复杂体系。逐步从定性的要求向定量的性能指标过渡,使混凝土可泵性的评价方法更趋合理、更科学,是我们当前应该追求的目标。用坍落度和压力泌水率来评价混凝土的可泵性,只能在试验室进行。在施工现场,用坍落度筒和秒表对入泵前的混凝土进行测试,通过简单定量,对混凝土可泵性进行定性分析,这对提出改善混凝土可泵性的具体措施具有参考意义。
【推荐】
【资讯】2016年中国桩工机械年会在北京
【新闻】三一重工贺东东:共同打造工业
【业界】中国工程机械行业进入新常态