凝土质量通病防治的应用已成为混凝土施工中必不可少的环节,搅拌站的混凝土在拌制过程中常容易出现或这或那的问题,给施工进度及施工质量带来麻烦。现就搅拌混凝土常出现问题的原因加以分析,并给出一系列解决途径。
1、泵送混凝土塌落度损失、坍落度不稳定问题的原因及解决方法
1.1产生原因
(1) 混凝土外加剂与水泥适应性不好引起混凝土塌落度损失快。
(2) 混凝土外加剂掺量不够,缓凝、保塑效果不理想。
(3) 天气炎热,某些外加剂在高温下失效;水分蒸发快;气泡外溢造成新拌混凝土塌落度损失快。
(4) 初始混凝土塌落度太小,单位用水量太少。
(5) 工地现场与搅拌站协调不好,使罐车压车、塞车时间太长,导致混凝土塌落度损失过大。
(6)混凝土搅拌称量系统计量误差大,不稳定。
(7)粗、细骨料含水率变化。
(8)水泥混仓存放,混合使用。
1.2 解决途径
(1) 调整混凝土外加剂配方,使其与水泥相适应。施工前,务必做混凝土外加剂与水泥适应性试验。
(2) 调整砼配合比,提高或降低砂率、用水量,将混凝土初始塌落度调整到200mm以上。
(3) 掺加适量粉煤灰,代替部分水泥。
(4) 适量加大混凝土外加剂掺量, 外加剂中调整缓凝成份(尤其在温度比平常气温高得多时)。
(5) 防止水分蒸发过快、气泡外溢过快。
(6) 选用矿渣水泥或火山灰质水泥。
(7) 改善混凝土运输车的保水、降温装置。
(8) 计量设备的精度应满足有关规定,并具有法定计量部门签发的有效合格证,加强自检,确保计量准确。
(9) 加强骨料含水率的检测,变化时,及时调整配合比。
(10)进库水泥应按生产厂家、品种和标号分别贮存、使用。
1.3 总结经验
针对泵送混凝土特别是泵送混凝土以及水下灌注桩基混凝土坍落度损失的问题。通过学习摸索试验总结出了一套结合实际情况解决问题的办法。如沟通外加剂厂家改善和调整外加剂中的缓凝成份;调整混凝土的施工时间,尽量避免不在高温情况下施工;在施工便道路况差路途远的情况下采用外加剂的二次投料;使用大掺量粉煤灰混凝土配合比施工等。使混凝土坍落度损失这一棘手问题,得到较大缓解。无论何种原因导致的坍落度变小造成无法泵送或是满足不了施工要求的坍落度的情况我们都能用外加剂进行调节使之达到所需坍落度,杜绝随意加水增大坍落度的不良习惯从根本上确定了混凝土的质量!
2、混凝土易出现泌水、离析问题的原因及解决方法
2.1 产生原因
(1)水泥细度大时易泌水,水泥中C3A含量低易泌水,水泥标准稠度用水量小易泌水。
(2) 水泥用量小易泌水。
(3) 低标号水泥比高标号水泥的混凝土易泌水(同掺量)。
(4) 同等级混凝土,高标号水泥的混凝土比低标号水泥的混凝土更易泌水。
(5) 单位用水量偏大的混凝土易泌水、离析。
(6)混凝土混合物温度过高,尤其夏天,气温高,水化反应快,坍落度损失大。
(7) 强度等级低的混凝土易出现泌水。
(8) 砂率小的混凝土易出现泌水、离析现象。
(9) 连续粒径碎石比单粒径碎石的砼泌水小。
(10)混凝土外加剂的保水性、增稠性、引气性差的混凝土易出现泌水。
(11)超量掺混凝土外加剂的混凝土易出现泌水、离析。
(12)部分型号的搅拌运输车搅拌性能不良,经一定路程的运送,初始出料时混凝土混合物发生明显的粗骨料上浮现象。
(13)混凝土搅拌运输车拌筒内留有积水,装料前未排净或在运送过程中,任意往拌筒内加水。
2.2 解决途径
(1) 根本途径是减少单位用水量。
(2) 增大砂率,选择合理的砂率。
(3) 炎热夏季,采取措施降低混凝土混合物的温度。
(4) 增大水泥用量或掺适量的Ⅰ、Ⅱ级粉煤灰。
(5) 采用连续级配的碎石,且针片状含量小。
(6) 改善混凝土外加剂性能,使其具有更好的保水、增稠性,或适量降低砼外加剂掺量(仅限现场),搅拌站若降低混凝土外加剂掺量,又可能出混凝土砼塌落度损失快的新问题。
(7)混凝土搅拌运输车在卸料前,应中、高速旋转拌筒,使混凝土混合物均匀后卸料。
(8)加强管理,对清洗后的运输车拌筒,须排尽积水后方可装料。装料后,严禁随意往拌筒内加水。
2.3 总结经验
针对混凝土易出现泌水、离析问题。通过学习摸索试验总结出了一套结合实际情况解决问题的办法。如优化配合比、加强原材料的进场检测、加强现场管理。杜绝因搅拌站现场管理不善而随意增加用水量的现象。
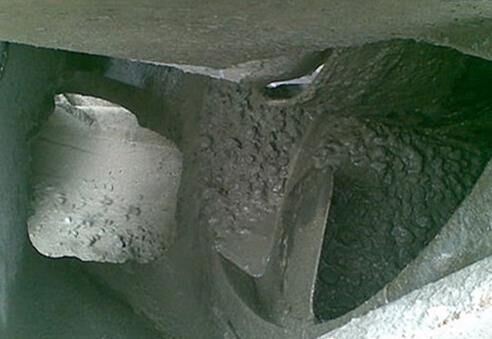
3 、混凝土可泵送性差出现抓底或板结的原因及解决方法
3.1 产生原因
(1)配合比选择不符合泵送工艺对混凝土和易性的要求。
(2)水泥用量偏低。
(3)砂、石级配不合理,空隙率大。
(4)配合比中砂率过小,坍落度过大,混凝土易离析。
(5)严重泌水的混凝土易出现抓底或板结(粘锅)。
(6)水泥用量大的混凝土易出现抓底现象。
(7)混凝土外加剂掺量大的砼易出现抓底现象。
(8)砂率小,混凝土易出现板结现象。
(9)混凝土外加剂减水率高,泌水率高,保水、增稠、引气效果差的砼易出现抓底或板结现象。
3.2解决途径
(1)减少单位用水量。
(2)提高砂率。
(3)掺加适量的掺合料如粉煤灰,降低水泥用量。
(4)降低混凝土外加剂的掺量。
(5)增加混凝土外加剂的引气、增稠、保水功能。
4、混凝土强度不够,均质性差原因及解决方法
4.1 产生的原因
(1)搅拌机计量设备故障,坍落度失控,混凝土强度离散性大。
(2)水泥过期或受潮,活性降低;砂、石集料级配不好,空隙大,含泥量大,杂物多,外加剂使用不当,掺量不准确。
(3)混凝土配合比不当,计量不准,
(4)施工中随意加水,使水灰比增大。
(5)混凝土加料顺序颠倒,搅拌时间不够,拌合不匀。
(6)冬期施工,拆模过早或早期受冻。
(7)夏季施工,试件未及时覆盖、养护。
(8)混凝土试块制作未振捣密实,养护管理不善,或养护条件不符合要求,在同条件养护时,早期脱水或受外力砸坏 。
4.2 防治措施
(1)水泥应有出厂合格证,新鲜无结块,过期水泥经试验合格才用。砂、石子粒径、级配、含泥量等应符合要求,严格控制混凝土配合比,保证计量准确,混凝土应按顺序拌制,保证搅拌时间和拌匀。防止混凝土早期受冻,冬朋施工用普通水泥配制混凝土,强度达到30%以上,矿渣水泥配制的混凝土,强度达到40%以上,始可遭受冻结,按施工规范要求认真制作混凝上试块,并加强对试块的管理和养护。
(2)加强计量设备的保养,确保投料准确,控制出机混凝土混合物坍落。
(3)施工现场取样应在搅拌运输车卸料过程中的1/4~3/4之间抽取,数量应满足混凝土质量检验项目所需用量的1.5倍,且不得少于0.02m3。人工插捣成型试块,应分两层装入试模,每层装料厚度大致相等,每层插捣次数应根据试件的截面而定,一般每100cm2截面积不少于12次。
(4)加强试块养护,标养试件成型后覆盖表面,以防水分蒸发、脱水,隔天拆模后,应放入温度为20±1℃、湿度为95%以上的标准养护室中养护。当无标养室时,混凝土试件可在温度为20±3℃的不流动水中养护,水的pH值不应小于7。
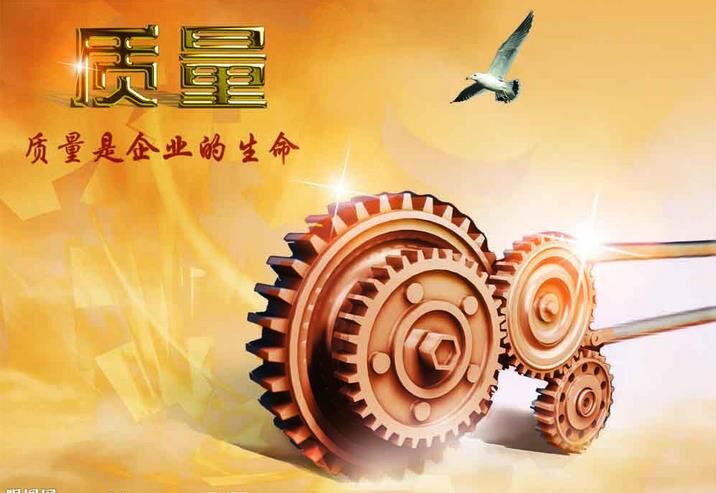
5、搅拌站质量控制经验及建议
混凝土质量管理控制中不可缺少是混凝土质量检验,是保证混凝土质量的主要手段。在混凝土的生产、运输直至施工的全过程中,它具有不可忽视的作用,它的主要作用有以下五点:
5.1把好五关、监督三不准:即原材料检验关、配合比设计关、计量关、混凝土搅拌时间关、坍落度及强度关;不合格的材料不准使用,计量不准的设备不准生产,不合格的混凝土不准出厂,确保混凝土符合质量要求。
5.2严格按规范规定随机取样,制作试块,如实出据报告,以真正起到指导生产的目的。
5.3做好事前控制,预防质量事故,通过对原材料和新拌混凝土的质量检验和生产全过程的质量监督,及时掌握混凝土的质量动态,及时发现问题,及时采取措施处理,预防发生工程质量事故,使混凝土的质量处于稳定状态。
5.4反馈信息,通过对检验资料的分析整理,掌握混凝土的质量情况和变化规律,为改进混凝土配合比设计,保证混凝土质量,充分利用外加剂和掺合料,降低成本,加强管理等方面,提供必要的信息和依据。
5.5加强质量培训工作,提高操作人员的技术水平和质量意识,增强工作责任心,保证混凝土质量合格。对混凝土搅拌站的技术人员和操作人员定期开展有重点的技术培训,这无疑对节约成本、提高效益和进一步保证混凝土质量都会起到比较明显的效果。
【推荐】
【业界】“智能风”席卷工程机械行业
【业界】京津冀一体化助推工程机械行业
【新闻】中国施工企业管理协会召开第31