外观质量是混凝土结构工程的重要属性之一,也是清水混凝土工程最被关注的一项指标。混凝土原材料经过拌合、浇筑、振捣和养护等过程,混凝土内起着填充作用的胶凝材料---水泥浆包裹着骨料,使得水泥的本色主导混凝土构件表面的颜色[1]。除了水泥的本色,混凝土最终呈现的颜色与其表面结构(如表层密实程度、平整程度及孔隙结构)有关[2,3],也与表面混凝土含水率等因素有关。外观质量一致性是评价混凝土建筑工程质量的重要标准。
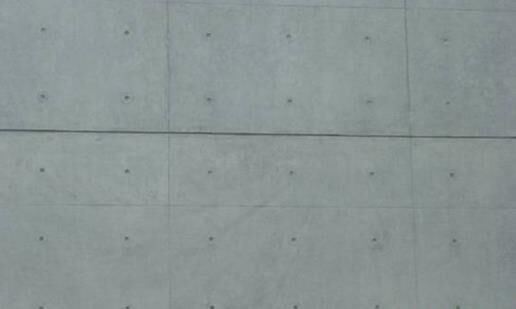
而混凝土表面色差是最容易被识别的混凝土结构外观缺陷之一,减少表面色差一直是实际混凝土结构工程的难点。混凝土外观颜色或深或浅,色差区域面积或大或小,严重影响着混凝土的外观质量,已成为影响工程创优的一大障碍[4-6]。
鉴于此,本文详细介绍导致混凝土结构表面出现色差的原因,并就混凝土色差的防治问题提出可操作性的有效措施,希望对实际工程预防混凝土表面色差现象,提高混凝土结构外观质量有所裨益。
2 混凝土表面色差的成因
2.1 原材料
2.1.1 胶凝材料
水泥工厂因工艺、技术及原材料来源不同,导致其生产的水泥存在质量不稳定的现象。水泥质量不稳定主要表现在两个方面。一是水泥细度变化大,其中水泥颗粒太细会造成水泥单位需水量变大,达到相同工作性时,混凝土水灰比也随之增大,进而使得混凝土局部表面颜色发生变化,引起色差;二是水泥化学成分出现波动,水泥中氧化铁和氧化镁的含量不同,影响水泥本身的颜色,同时氢氧化钙等水化产物生成量存在差异,可进一步导致混凝土表面出现色差。
同理,混凝土中掺加的矿物掺合料的种类、细度、化学成分、烧失量等的变化,同样会导致混凝土表面出现色差;掺合料计量不准引起的实际掺量发生变化,也会导致混凝土表面出现色差。
2.1.2 骨料
针片状石子含量高,不仅会影响混凝土的流动性,也可导致水分分布不均,使得混凝土表面颜色产生不均匀现象。另一方面,粗、细骨料中含泥量较高,也会导致混凝土的颜色加深[7]。
2.1.3 拌合水
拌合水对混凝土外观有一定影响。被污染的河水、地下水等,因含有高价金属离子,或油污、表面活性剂等,会通过影响混凝土用水量的稳定性、含气量以及生成显色氧化物等,导致混凝土表面产生色差。
2.2 新拌混凝土现场状态
混凝土拌和物工作性出现异常,会导致混凝土产生色差现象。新拌混凝土发生离析后,内部各种组分不均匀沉降,伴随而来的是混凝土中水和外加剂以及密度较小的粉煤灰等掺合料在混凝土表面的富集,使得混凝土的表面颜色与正常混凝土之间产生差异。在实际工程中,外加剂和水泥相容性差时可能导致混凝土产生滞后泌水现象,很易引起混凝土产生色差。混凝土内部泌出的自由水向上运动,同时带走大量的水泥浆,致使上部混凝土中水泥浆的总量显著高于底部。根据文献[1,4],水泥浆相对含量越多则生成氢氧化钙晶体(呈白色)的量越多,造成混凝土结构上部的颜色比下部浅,因而产生显著深浅“分层”。
另一方面,在混凝土结构物的施工缝附近也会产生色差现象。如呈条带状的斑块,俗称水线,对混凝土结构物的外观有较大影响。其主要形成原因如下:
1) 工地浇筑作业不连续。
2) 施工中遇到雨水等原因造成混凝土表面局部有积水现象。
3) 在振捣过程中振动棒有时会碰到模板。模板受到振动后会产生缝隙,积水就沿着缝隙往下流,带走水泥浆体而形成一条条松弱的流水痕迹(即水线)。另外,模板接缝不严密也会导致漏浆,漏浆带走砂浆和水泥浆也会造成水线。
4) 相邻两层混凝土浇筑时间间隔太长。在混凝土分层浇筑过程中,在第一层混凝土振捣完毕后,顶面产生较多砂浆(甚至净浆)。若第二层浇筑时间太晚,比如当第一层混凝土已处于半初凝状态时,才开始浇筑第二层混凝土。这时很难将第一层混凝土顶面中较多的砂浆与第二层混凝土混合均匀。而相对于整体混凝土而言,这部分砂浆的颜色是有偏差的,导致混凝土结构在施工缝处产生色差[8]。
2.3 模板及脱模剂
由于结构混凝土浇筑所采用的模板不太可能是整体模板,模板拼接后存在接缝。不论是钢模板还是木模板,由于制造、使用、保养等都会使模板存在(产生)一定变形,所以模板之间的接缝往往不严密。混凝土在浇筑过程中,会透过不严密接缝漏浆、漏水,导致混凝土上下分布不均,引起色差。
实际工程中,钢模板锈斑污染可直接影响混凝土表面的颜色。这是由于模板在潮湿环境中会发生锈蚀,锈蚀产物(即铁的氧化物)很容易粘附在混凝土表面,形成锈斑,且颜色多呈黄褐色,严重影响混凝土表面颜色。
另外,工地使用的脱模剂种类也很多,质量参差不齐。常用的油质脱模剂都具有一定的着色作用,可污染混凝土表面。例如,当采用柴油作脱模剂时,混凝土表面颜色多发暗;而采用机油作脱模剂,混凝土表面颜色有发白现象。
2.4 外界环境
由于混凝土材料既亲水又亲油,因而是一种极易受到污染的材料,尤其在污水处理厂、发电站和重工业区等污水、烟尘和粉尘较多的地方,往往被污染得很严重。
另一方面,水泥的水化反应过程与环境温度有较大关系。当环境温度较低时,水化反应较慢,强度增长较慢,混凝土达到较高强度花费的时间较长,水化反应充分,析出的氢氧化钙较少,因此混凝土成型后的外观颜色就呈现青色。相反,当温度较高时,混凝土原料吸热较多,温度较高,混凝土入模温度较高,水化反应较快,较高的水化热致使混凝土内部温度迅速升高,析出的氢氧化钙较多,颜色趋向于灰白色。因此,在连续浇筑施工情况下,往往由于不同部位浇筑时环境温差较大而引起色差。
3 混凝土色差控制措施
3.1 严格控制混凝土原材料质量
针对原材料质量的控制,可采取以下措施:
1)严格控制水泥来源,避免不同厂家不同种类的水泥混用。所用水泥必须选用生产工艺先进,生产供应能力强的厂家,保证其质量长期稳定,组分不发生剧烈波动。
2)加强水泥颜色的检测。要求现场每进一批水泥,都要对其颜色进行目测对比,并与混凝土本色进行对比,当不同批次间水泥的颜色发生较大变化时,应予以更换。
3)严格控制矿物掺合料的来源,保证品种、等级、细度、化学成分和颜色的稳定性,当不同批次间矿物掺合料的颜色发生较大变化时,应予以更换。
4)严格按照有关规范进行减水剂(或/和其它外加剂)与水泥适应性的检验,要求通过调整减水剂产品各成分含量比例,以提高其与水泥的适应性。
5)控制砂石料的含泥量、泥块含量及含水率,确保砂石料含泥量、泥块含量符合要求,可有效控制混凝土色差现象的出现[9]。
6)严格控制拌合水的来源,按标准检测拌合水的性能,不得使用有污染的河水和地下水。
3.2 严格控制混凝土浇筑质量
浇筑和振捣混凝土时,应尽量减少与钢筋等内埋物件的冲撞,避免混凝土骨料与浆体分离。若浇筑高度过高或钢筋过于密集,应采取加串筒、溜槽等减少冲力的措施。同时,粘附于模板上的骨料和浆体分离后易造成石子跑边、堆积,因此应尽量避免飞溅。因包裹石子的浆体过少,振捣过程中不流动或流动性差,容易产生蜂窝和显露石子痕迹的颜色深浅不一的花斑纹。在混凝土浇注过程中应确保混凝土的和易性及均质性,不得随意加水或更改材料用量,同时要确保混凝土的连续浇注,如中断时间过长,虽未超过混凝土的初凝时间,但极易在结合面之间形成水印及青白颜色的色差。对于采用全面分层及分段分层浇注的混凝土,浇注前要计算分层用量和混凝土供应速度,同时掺加缓凝剂以延长混凝土的初凝时间,避免出现间断色差[6,10]。
在连续施工过程中,还应尽量减少施工环境温度的影响,如在夏季施工时可以采取降低入模温度、设置冷却水管等方式来降低混凝土内部温度,将每次浇筑的混凝土的温度控制在较小的温度范围内。
3.3 使用优质的脱模剂
长期使用掺机油或柴油的脱模剂,钢模容易发生锈蚀,故应禁止在脱模剂中掺机油或柴油。应采用有防腐、防锈功能的优质混凝土脱模剂,其可以保护钢模,使混凝土更易脱离钢模,有利于提高混凝土外观质量,有效防止混凝土表面产生黑斑或污迹。目前施工中使用较多的是环氧树脂型脱模剂,其具有不污染混凝土、表面光洁等优点,可有效减少混凝土产生色差的概率。
3.4 加强钢模的防锈及处理
新出厂或长期不使用的钢模,一定要对内胆做好防锈处理,可采用涂抹有抗氧化、防锈功能的液压油等措施。搬运、存放和拼装模板,以及安装钢筋网笼时,严禁撞、碰、砸伤钢模内胆。必要时可采用磨光机对钢模内壁进行打磨,把钢模内的水泥浆彻底清除,使钢模内胆保持平滑,从而提高混凝土外观质量。
3.5 混凝土养护
养护应采用统一的养护方法,保持混凝土养护条件一致,避免因养护条件不同而造成的色差。洒水养护时应洒水均匀并清除外表污物,不得采用易掉色的覆盖物。应做好成品混凝土的保护工作,防止污染、碰撞和划伤等[10]。
清水混凝土、装饰混凝土等对表面质量要求较高的混凝土,应尽量远离污染源(粉尘、青苔和污水等),净化空气质量,以保护混凝土颜色不受或少受侵害。
4 结语
随着人们生活水平的提高和审美观的进步,混凝土结构外观质量越来越受到关注。为了提高混凝土构件的外观质量,同时又能满足经济、美观、耐久的使用要求,应当从多方面入手。在实际生产过程中采取本文所述措施,混凝土表面色差现象能够得到有效控制效果显著。但需注意的是,国内外对于混凝土色差的研究并不多,且多采用控制变量法对比原材料差异、环境温度与浇筑制度等对混凝土产生色差程度的影响,具有一定的经验性,尚无法揭示色差产生的本质原因。相关研究结论的普适性及应用的广泛性有待验证。
因此,对混凝土色差产生的机理与相关防治措施的进一步研究是十分必要的。
【推荐】
【新闻】中联重科斩获9亿元大单 在工程
【业界】重磅!28国元首、政府首脑确认
【新闻】关于开展2017年度工程机械行业